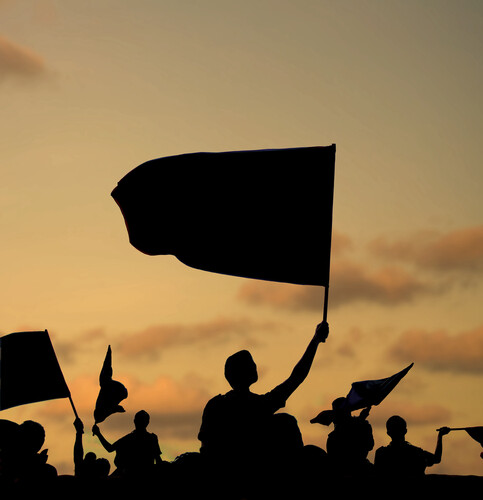
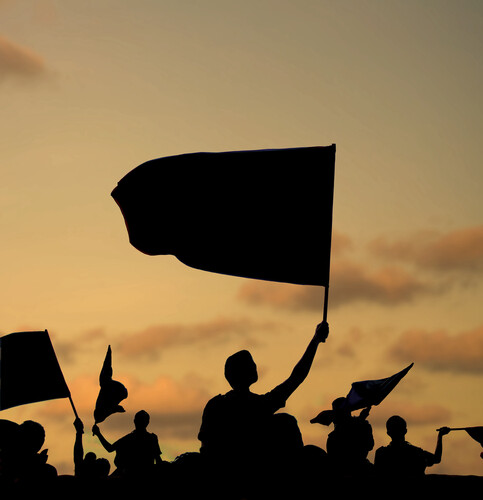
The Industrial Internet will pose some serious challenges before it is common in the manufacturing industry. First of all, turning a factory into a smart factory requires a large investment and a new way of working. It will also require big data standards and an ecosystem to ensure smooth operation between different companies, which has yet to be developed. OF course, the vast amount of sensors in the machinery will create a lot of data, driving, probably driving us into the brontobytes era pretty soon. This will require powerful analytics that can handle that vast amounts of data. In addition, security of all the data becomes a vital issue for continuation of the factory as malware in the Industrial Internet could trigger direct physical destruction instead of ‘just’ affecting sensitive information. The Industrial Internet is just one of the benefits of applying big data in the manufacturing industry, so let’s have a look at the possibilities.
To optimize operational efficiencies
Using data during the production process and sensors attached to machines, the entire production process can be analysed to understand how each section is performing. The moment a process deviates from the standard, an alert can be created to inform the factory what is going on. Mistakes can be found much faster and errors or bottlenecks can be solved earlier. The sensors can inform an engineer what the problem is, so he or she knows better what to do in order to fix a problem faster. With big data technologies it is also possible to model the production of the industrial products virtually and optimize the production process. When all this information is made visible in one central dashboard, transparency is created that can help manufacturers improve their production process.
In addition, many organisations have their data in silos across the company. Especially in large multi-national organisations, this information can be difficult to retrieve across the company. Big data can help organisations centralize all information into one platform (in the cloud), giving access to all employees to the relevant information based on their role. Creating a product life cycle management (PLM) platform that integrates datasets from multiple systems will significantly increase effective and consistent collaboration across the organisation.
When information is accessible from a centralized platform in the cloud, it will ensure that all departments everywhere throughout the organisation will work with the same data. This will decrease the amount of errors and as such increase operational efficiency. Operational efficiency will also be increased when data sources from relevant suppliers are taken into consideration. Suppliers can better know when to deliver what materials.
To optimize the supply chain
Large OEM’s can have 1000s of suppliers delivering 10.000s of different products to manufacturers, each will trade at its own price, depending on market forecasts and many different other variables such as sales data, market information, events and news happening in the world, competitor data and weather conditions. Using sales data, product sensor data as well as data from the supplier database, industrial manufactures can predict the demand accurately in different regions around the world.
Being able to track and predict inventory and prices and to buy when prices are low can significantly reduce costs for manufacturers. If they also know, using the sensors in the products, when products are about to break down and which part are needed where, they can forecast which parts are needed where and when. This will bring down inventory and optimize the supply chain for manufacturers even more. Collaboration with different players within the supply chain can help to shape demand at the manufactories to deliver a better B2B experience.
To save money
Centralized monitoring of all processes during the manufacturing of the equipment using sensors can also show anomalies or peaks in the energy consumption, which can be used to optimize energy consumption during the production process. For example buildings that are too warm or too cold based on the amount of people present. Analysing all processes can result in a significant reduction in energy consumption.
The Industrial Internet, where the manufacturing companies use big data technologies to improve operational efficiencies, reduce costs and create better products offers a lot of possibilities. Within the coming years, more organisations within the manufacturing industry will see the need to optimize the supply chain and operational processes using big data, helping the Industrial Internet as envisioned by GE to become reality.
image: revolution/shutterstock