Analytics technology has seriously disrupted the manufacturing industry over the last decade. According to Mordor Intelligence, the market for analytics in manufacturing will be worth $19.5 billion by 2028.
There are a number of ways that analytics has helped manufacturing companies improve their bottom line. We have pointed out that it can ideal for forecasting future demand and get a better understanding of market trends in one of our articles on using analytics for improving marketing in manufacturing.
However, there are a lot of other major benefits of using analytics to optimize the business models of manufacturing businesses. One of the major advantages of analytics is that it can help manufacturing companies produce goods more effectively, more quickly and with fewer defects.
This is especially true when it comes to creating the exoskeletons of robots. We alluded to this benefit in our article Invest in Analytics to Improve Your Production Line. Keep reading to learn how this process is changing in light of advances in analytics.
Designing and machining exoskeleton robot needs a lot of machining expertise, now a days with the advent of modern machining technologies designing and developing more precise exoskeleton robots is quite easy. These machining techniques enable the engineers to figure out the perfect material consideration and structural stability of the robots. With the help of modern machining tools engineers are working on designing complex and highly effective designs that enhance human mobility, strength augmentation, and functional versatility.
Modern machining techniques such as 3-D printing and 5-axis CNC machining, help engineers and designers to create complex geometries. These advanced machining innovation helps in creating lightweight structures, that improve the agility of the robots. Further in this article, we will explain the role and amazing innovations of using advanced machining processes in different aspects of developing exoskeleton robots.
Machining Challenges in Prototyping and Iterative Design
Developing a prototype that meets the functionality requirements is a complex task. A lot of repetition and design alterations are needed to figure out a perfect design that meets all the functional and structural requirements. In conventional machining practices, the prototyping stage can cause a severe headache to you. It is a fact that facing the machining challenges is an integral aspect of designing and developing this exoskeleton machinery. Fortunately, analytics is helping significantly.
For engineers and designers achieving high precision and tight tolerance is the most important paramount. This type of machinery often consists of small and complex intricate parts, these parts require high precision to ensure optimal performance. To gain this high precision engineers need to do some iterative adjustments to refine the design based on performance feedback.
Advanced CNC machining and 3D-printing technology helps a lot in gaining design alterations and give a chance to test different materials and designs. The main motive of engineers is to develop a structural frame that is lightweight and has durable structural strength. In this perspective, engineers have to test different materials and find optimal combinations for strength, weight, and durability.
The implementation of these advanced machining techniques helps in developing exoskeleton robots that have high functionality, structural durability, patient adaptability, and user comfort in this rapidly advancing field.
Tolerance Management in Machining for Exoskeleton Joint Mechanisms
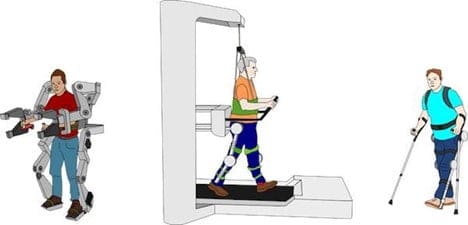
The basic purpose of the exoskeleton structure is to develop machinery that can assist user’s daily body movements and enhance their lifestyle. This paramount can only be achieved if the manufacturers ensure tight tolerance in the exoskeleton joint mechanism. Tolerance management is a crucial aspect for ensuring reliable functionality in exoskeleton machinery so that it facilitates natural human movements. CNC machining is a main player in it, this high level of precision can only be achieved through advanced computer numerical control machining.
For a better understanding of the importance of tolerance in intricate joints, let’s consider the example of the Lower Rib Hip Exoskeleton. The exoskeleton is the hip joint structure of the human body, the hip joint consists of a ball and socket interface and it allows flexion, extension, abduction, and adduction. Due to the weight of the body, the hip joint needs a lot of structural stability. This joint needs a tight tolerance and it can only be achieved by the CNC machining. CNC machining along with CAD modeling enables a perfect design for the socket part of the joint for optimal performance.
Now for the ball component of this joint mechanism, which is desired to articulate within the socket. For a smooth motion within the socket structure, the ball needs to be perfectly precise and the tolerance should be minimal. The CNC machining enables to manufacture of a perfect ball component as per the desired tolerances as tight as a few micrometers. And for the socket, which will be machined to mirror, these tolerances will be a snug fit that minimizes any play in the joint.
In this way, tolerance management in exoskeleton machining is performed so that engineers can ensure a perfect biomechanical structure, that assists the user with perfect ergonomic design.
Machining Integration for Sensor-Embedded Exoskeleton
Sensor and adaptive feedback systems are critical aspects for enhancing functionality and performance in exoskeleton robots. The accurate reading through these sensors enables the designers to keep enhancing the biomechanical structure of these robots. The sensor system along with a control unit needs a desired specific space for its installation and way in the robot for wiring or feedback system. The Precision machining techniques allow to create of accurate housing along with intricate pathways. These pathways ensure tidy and efficient integration of sensors.
For a better understanding of machining challenges in these robots, exemplify the installment of pressure embedded system in exoskeletons. The pressure sensors are placed under the feet to judge the motion of the body. For better feedback from these sensors they must be placed in such a way so that they are able to read even a slight movement and it will only be possible if they are distributed evenly. For that reason an intricate pathway is created through CNC machining which enhances the exoskeleton’s responsiveness to user movement.
In sensor embedded exoskeletons another important aspect is protective layers. The sensors and the control unit is highly sensitive to environmental conditions, they may be damaged or start giving wrong reading to control units if they get humidified. For that reason, protective layers are manufactured by the help of advance precision machining, mostly through multi axis machines so that they ensure smooth operations in sensors. These protective layers are made from aluminum and polymer alloys and machined as per specific shape of the joints.
Surface Finishing for Enhanced Wear Resistance
As the exoskeleton robots consist of a lot of intricate joined parts, mostly these parts are ball and pin joints. It is a fact that these type of joints under several load bearings conditions often face wear and friction issues. If these issues come in these robots, they cause lag in their motion.
To overcome these issues, an appropriate coating and surface treatment technique is used to enhance the agility and lifespan of these machinery. Several finishing techniques like Physical Vapor Deposition, Chemical Vapor Deposition, Polishing and precision machining contribute to eliminating these issues. Mirror-finish polishing, which is achieved through precision machining and abrasive process helps in reducing surface irregularities.
Conclusion
Summing things up, the machining techniques play a pivotal role in maintaining the biomechanical shape of the exoskeleton robots. The techniques help to maintain tight tolerance between joints and precise movements of the exoskeleton parts so that they can ensure ergonomic movements as per human nature. The machining techniques implemented on exoskeletons need expert engineers and designers for machining its complex parts so one should be well aware of the machining capability of the chosen machining shop.